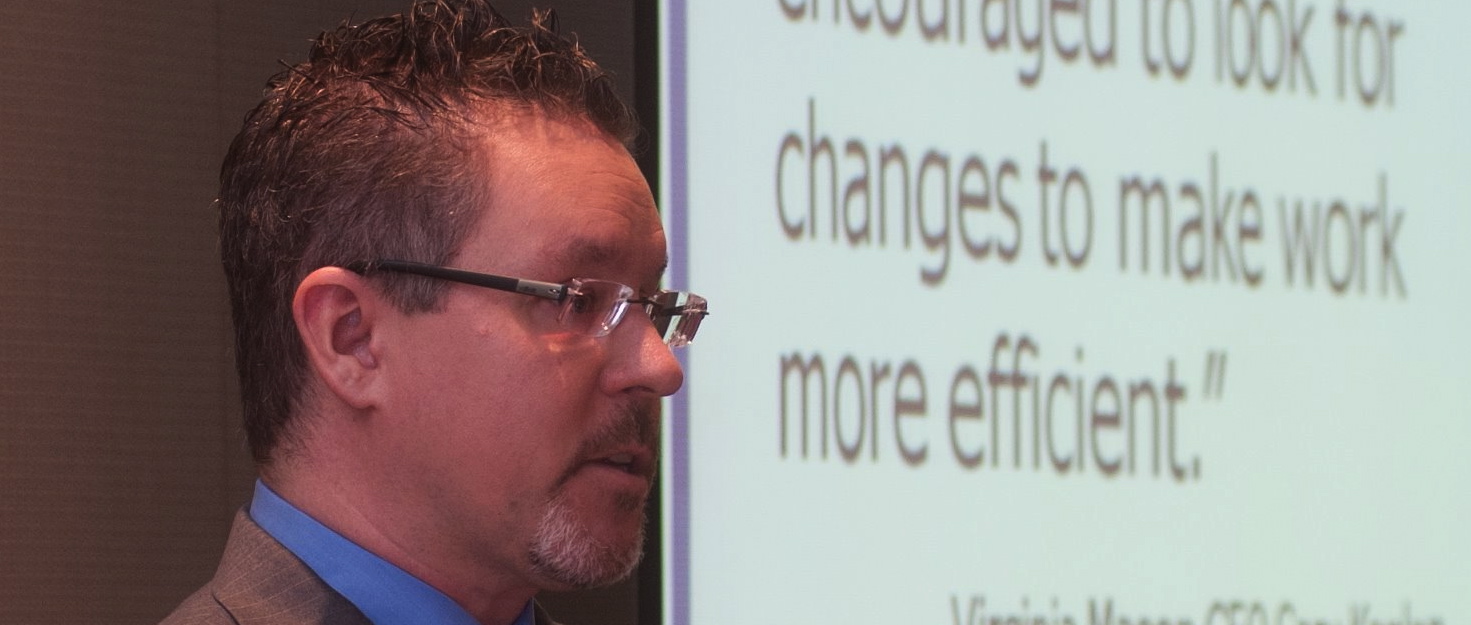
Contact Mark to bring a workshop to your organization.
“Psychological Safety and Continuous Improvement“
What is Psychological Safety?
Why is it a foundation (or a pre-condition) for continuous improvement?
Mark Graban has workshops that can help!
Learn more
“Better Metrics” — (a.k.a. “Measures of Success“)
- This interactive workshop helps you and your leaders do a better job of leading through the optimal use of performance measures.
- Learn best practices for managing and reacting to performance measures appropriately (including “Process Behavior Charts”).
- Avoid common mistakes that can slow improvement, demoralize teams, or hamper your Lean journey.
Learn more
“I can’t look at the typical charts and graphs the same way anymore after that workshop!”
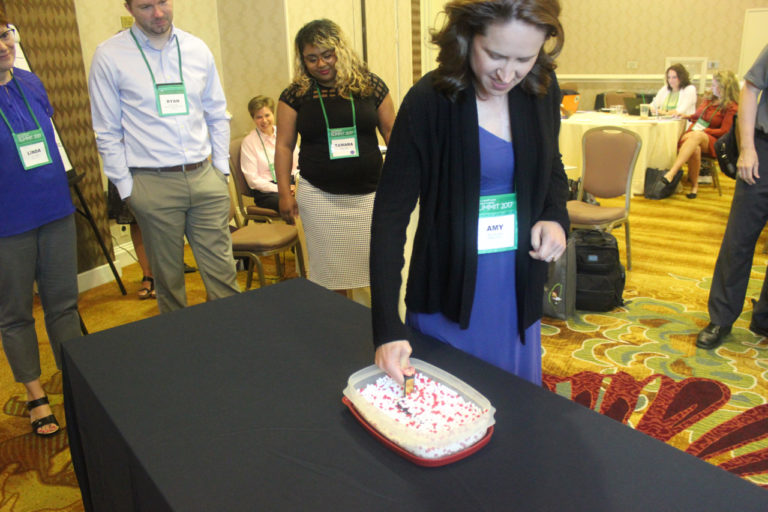
“Mark made complex ideas simple to understand”
“Healthcare Kaizen“
- Public Workshop summary (View full description as PDF)
Join speaker, author, and consultant Mark Graban for a small, intimate half-day seminar to learn about methods and practices from his book, Healthcare Kaizen: Engaging Front-Line Staff in Sustainable Continuous Improvements.
You might have heard about other healthcare organizations that are using Lean improvement practices. In particular, many health systems are using “Rapid Improvement Events” (aka “Rapid Process Improvement Workshops”) as a way of driving change. However, a growing number of organizations are also embracing “daily Kaizen” — or a process to facilitate small, meaningful changes as an ongoing continuous improvement methodology. If your organization has not yet started “going Lean,” then daily Kaizen is a great way to get started before making the leap into larger events.
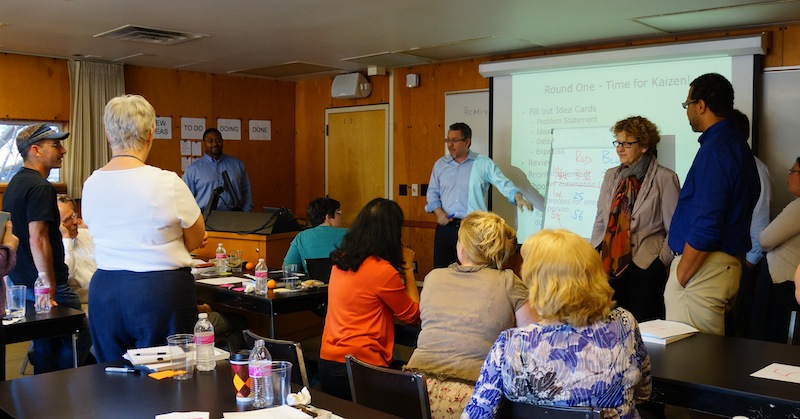
Attendees will learn through lecture, discussions, and a hands-on exercise that brings the Kaizen improvement methodology to life in a fun way. Registration is limited to 20 people to ensure a high level of interaction.
A comment from an attendee after putting these ideas into practice after the workshop:
I love the quote of one of our employees the other day: ‘We are great at identifying problems at [organization]. We just don't fix them. Now we feel empowered to fix things.'
(this is also a great onsite workshop since we can roll up our sleeves and start improving)
Feedback from an attendee / leader:
“That training was so awesome! You should see all the email traffic back and forth among the participants today. That was EXACTLY what we need to get people who were tepid at best about starting a lean project (not “LEAN”—that is what I learned!) to really look for opportunities to make changes. I cannot thank you enough for the really excellent training.”